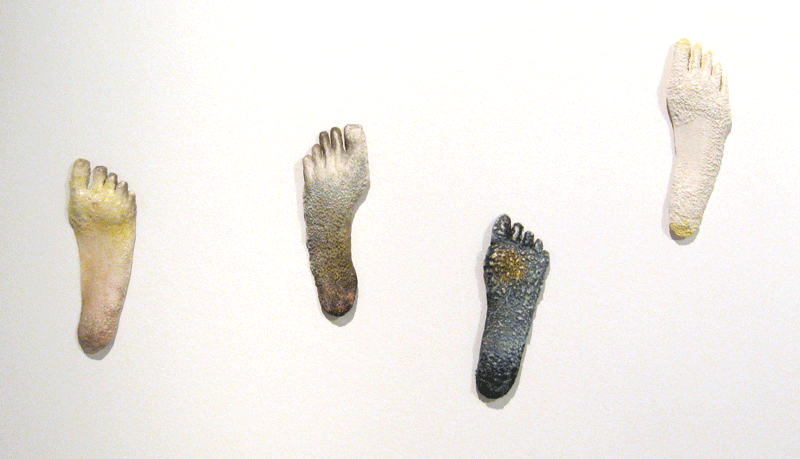
Silicon Footprints, Porcelain paperclay high fire glaze, then smoked/saggar/pit/torch, 2008 See more on this silicon footprint theme.
Eco-friendly Paperclay Practices for Makers Quick list
Some but not all forms in paperclay for installations or outdoor need not be fired. The high green strength of the pulp fiber and chance to work wet dry, repair, assemble makes transport easy. Clearly this practice saves emission and fuel. You can see examples of artist who avoid firing in my books.
HOWEVER
Lots of us (like me) require a FIRED light weight paperclay with every kind of color or glaze surface glazes, whether it be for tile, all weather, for pots, for long term sculpture or architectural detail. Always test fresh batch first just in case- your local situation is unique) It is an extra step to recycle ♻️ your own paper to pulp and mix it in with your favorite base clay recipe that fits your glazes.
🌐 1. ♨️ Single fire saves ⬇️ fuel 🔥, ⬇️ Power 🔌, ⬇️ TIME⏳, ⬇️ COST💰
Skip a bisque 📆 📆 fire, and apply glaze to bone dry which is tough enough to absorb some glaze if you dip, brush, spray. Do this in 5-10 mins before the paperclay form will re-soften eventually in water. Let the coats dry between applications if applying thick. Don't overdo too much wet too fast. Practice first to get the knack of it.
🌐 2. ♨️ FIRE fastER schedule ⬇️ fuel 🔥, ⬇️ Power 🔌, ⬇️ TIME⏳, ⬇️ COST💰
Little need to candle 🕯️ ♨️ kiln load over night for hours like typical. Water and air escape via the hollows inside the natural plant fibers of cellulose in pulp... Expect drying cracks if there is not enough pulp added. These need patch. Fast cycle works best with the higher proportion of pulp.
🌐 3. Fast dry works, and assemble wet dry, or dry to dry ⬇️ TIME⏳.
Resist the urge to baby works. (This reduces use of plastics for coverings. Wet or damp rags can substitute.) Force drying in open air, forces them to flex and shrink as they dry and expand if re-wetted. If find crack- REpair it before Fire.
Traditional leather hard stage assembly is not ideal or required with paperclay.
🌐 4. Avoid 🔌 ♨️ firing pots-forms from students/ or self with weak handles that will end up in shard pile. Easy fix to save firing ⬇️ TIME⏳ and fuel in classroom settings. Reduces frustration by learners who get a second chance to attach/join. Scrap from this can be
🌐 5. Aging is not needed like traditional clay since pulp is distributing water deep inside to every particle efficiently. This happens ⬇️ TIME⏳ during reclaim slake down too. See next.
🌐 6. STORE SCRAPs of PAPERCLAY DRY Flatten paperclay scraps or slice to bread thin slice with wire let them dry totally as pancake, bread slice, burger shape for storage. I save in labeled in 📦 boxes- or bag.. Avoid thick balls of dry paperclay scrap they longer to slake- break down in water. End the stinky muck bucket. Reduce chance of mold, mildew etc which needs water to grow. Dry paperclay scraps slakes down quickly ⬇️ TIME⏳ in a bucket of water when ready for another work period.
🌐 7. ♻️ Reclaim scrap glaze with ♻️ SCRAP clay and turn it to ♻️ special paperclay. Fired clay color will be darker hue, but there's many interesting forms possible to make. The overall cone to fire to melting point- vitrification point will be lower because of so much glaze- test- the mix may end up a low fire version.
🌐 8. Maybe just build an air dry sculpture that doesn't need to be fired as some artists do. SAVE 📆 📆 too.
🌐 9. To keep a store-bought bag moist, I'll add a tablespoon of water to bag before sealing. Some can story a while, but better to use soon. Moist paperclay stiffens to leather hard at a certain point, better to slice it before it gets to leather hard to store it completely dry as in item 6 above.-
🌐 10. Consider lowering ⬇️ your 🔥 ♨️ firing temperature of your base clay to cone 4-6 oxidation instead of cone 10. About 20% more fuel and power are needed just to get your kiln from orange (cone 6) to white heat. (cone 10)
🌐 11. USE water 💦 to reduce airborne dusts, watch for ways to 💦 ♻️ RE-USE WATER. Pulp making water can be reused for various rinse, cleanup.
🌐 12. If mixing your own paperclay... Avoid adding so called "recycled" store bought dry pulp insulation (such as a building material) treated with any fire retardant which is law in some countries. Fire retardant additives like boron etc to pulp used in a paperclay, in fire generates 🔥 ♨️ TOXIC ☠️ foul fumes and extends the burnout smoking time about 6 hours all the way to the red heat. It seemed like a good idea but .... the foul air cause caused distress neighbors! Let that not happen again!